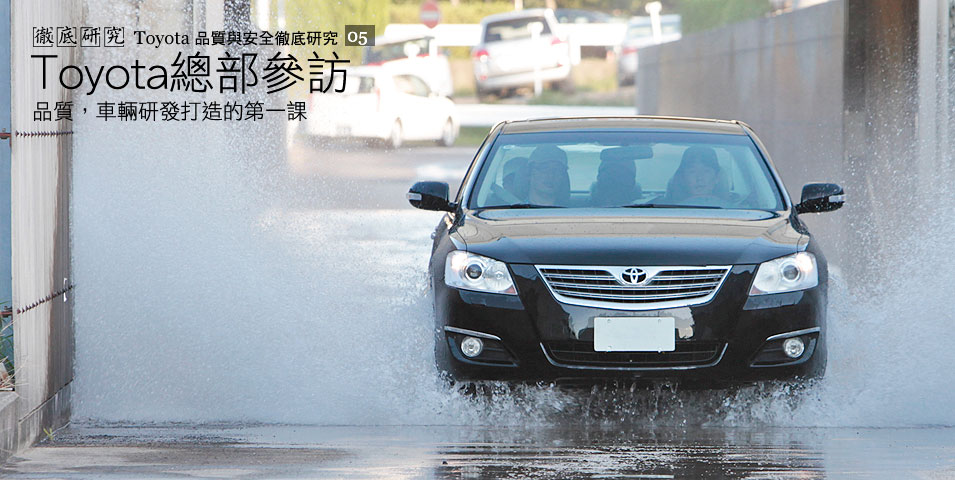
64,097
2010
11月
29
傳承,一個重要的傳遞過程,通常指涉將良善的文化、習慣或者是生產方式繼承而下。然而當 Sakichi Toyoda 豐田佐吉建立了豐田自動織機製作所,將豐田精神定義為品質第一的那一刻起,屬於豐田博大精深的企業內涵從此流傳而下。直到豐田佐吉之子 Kiichiro Toyoda 豐田喜一郎,於 1937 年創立了 Toyota 汽車公司,還是這樣告誡自己的員工,當時他說道:「充分了解客戶的需求,並且將改進反應在新的產品上,追求品質的精進。」而新產品服膺的兩個重要的基準,便是「Customer First 顧客優先」與「Quality First 品質第一」的經營之道。60 多年後的今日,以品質起家的 Toyota 汽車,在集團發展的路上仍舊追求著當年草創者的心血目標。
我們試著以簡單的 Toyota 生產流程圖,來點明車輛從研發到市場販售的時間動線。在車輛「設計與評估」→「進行量產」→「物流與銷售」→「發現與解決」的四點循環中,「顧客優先」與「品質第一」的經營之道,必須在車輛誕生前的設計、研發期便得履行,以完整車輛生產前的根基品質。在這個階段 Toyota 擁有完整的品質打造基本流程,以確保生產車輛的素質水準,接著才可將產品放行至大規模生產階段,並緊接著進行上市準備、市場銷售與產品再檢討。然本章節所要討論的焦點在於,車輛生產前的品質要求流程,介紹 Toyota 車輛研發期,為消費者所建立的重重關卡。
所以說車輛品質的實踐,必須追溯到甚至連車子的雛形都尚未孵化的研發期。在總工程師的運籌帷幄下,協調如造型設計、工程設計、底盤、引擎、懸吊設計、採購、協力廠商等各單位間的配合,並透過與顧客保持最密切關係的零售商及業務部門的交談,才能夠抓住客戶需求。工程團隊所設計的車輛,另外還得通過「商品監察」團隊的審核,「商品監察」是由消費者的立場來監察商品。因為車輛品質的完備必須建立在製作過程中,但是商品並不能以製造者的角度來打造,而必須以消費者的角度來確立。
商品監察串連著市場與工廠間的溝通熱線,再度把顧客優先與品質第一的最高訴求,擺在每位生產者的眼前,讓在研究室內的工程師團隊不僅只是一群訓練有術的專家,不知市場取向與民之所欲。如此,當產品在最初期的研發過程中,即能實踐環境理論,擁有正確的發展方向。再等到車輛進入實體打造、測試與評估階段後,所謂品質的考驗才正要開始。
然而車輛品質對消費者手中的那輛愛車最直接的反應,呈現在駕馭內容、系統良率與車輛耐用度上,隨即直接影響產品市場表現與銷售量。對於車廠來說,品質不外乎是生存於商業戰場上最關鍵的要點之一。Toyota 汽車公司自 1964 年起便為車輛品質進行一連串專屬測試,Toyota 將其稱為「Quality Insurance System in R&D Process 研發期實踐的車輛保障系統」,該系統擁有 7 大測試項目,主要模擬車輛產品出廠後所面臨的使用環境,並以極端嚴苛的測試方法,來達到產品的嚴格檢驗。以下,我們將為您清楚解釋 Toyota 所建立之品質 7 大測試項目:
身長在台灣的消費者,或許對車輛涉水的經驗並不陌生,有時夏日午後突如其來的雷陣雨加上排水不良的汙水系統,不一會兒,原有的道路就變成汪洋一遍!所以說駕車涉水而過,可以說是許多國內消費者的共同特殊經驗。在這項測試內,車輛將涉水通過一條特殊設計的水道,用以模擬日常生活用車時,車輛遇路面積水、穿越淺河、泥凝等狀況。測試目的在於確保產品不會因涉水、涉泥時發生停擺與故障,或是液體影響車輛電子系統,甚至由進氣孔道進入引擎內部。
Toyota 在各處測試場地內皆有多條水道設計,並可利用路面的斜角、坡度、起伏等狀況,來模擬不同的道路型態。在水量的深淺上亦可自由調整、甚至改變液體的特性或以泥濘來代替測試。而當車輛在駛入涉水測試時,Toyota 試車手每趟會採用不同速度前進,最快時速則基本保持在方便操駕的範圍內。
涉水測試對現代車輛來說已是普遍的測試項目,因此在車輛的設計過程中,配合車身造型、引擎蓋下的孔道設計、底盤處的孔道設計等,皆會讓水流順著車側自然劃過,避免液體直接灌入引擎進氣孔內。Toyota 慣於將引擎進氣孔設計在引擎室高度最上緣處,並在引擎蓋覆蓋下來後,緊連貼齊著蓋面。二來,引擎進氣孔道的特殊彎角設計,亦能在少量液體流入進氣孔後,避免直接灌入燃燒室。
當車輛徐步開出水道,完成涉水測試後,技師可由車輛是否正常運作,來初步判斷車輛功能正常與否。進而逐條檢視共 100 多項的指定流程、拆解車輛電氣零件,來確認車輛在涉水測試後的結果。
20 年前,Toyota 首創用於車輛測試之雪場風洞,該風洞不僅可製造人工雪片、暴風雪,更可將環境溫度調降至攝氏負 50 度,讓測試車輛完全覆蓋於冰雪之內。雪場風洞主要用以檢測車輛在低溫環境下的運作狀態,發現容易故障的零件、進行系統改進與檢修等。
於大太陽底下經過整日曝曬的愛車,把自己烤得如同一塊燒紅的鐵塊,車內的溫度更是高的嚇人,車輛承受得起陽光終日的摧殘嗎?我們來看看測試條件相當嚴苛的高溫測試。高溫測試是與低溫測試相反的測試方式,測試過程,將車輛置放於可加溫至攝氏 75 度的隔離室內,用以模擬世界上各處高溫地區。測試過程車輛並不僅僅是靜止擺放,而是需要配合高、低速行駛、徐進等狀態。測試目的在於檢測車輛於高溫環境中的作動過程,除了主要可檢驗引擎功能外,對於油料儲藏、剎車系統功能、車內外橡膠製品、皮製品的耐熱程度,皆可進行檢視與缺失改正。
在電信傳輸技術普遍且發達的今日,我們生活周遭佈滿著如雷達、無線電、手機、電塔、軍用電波等長短電磁波,其在我習以為常的便利生活中,成為不可缺少的通訊物質。不過比如說收音機、手機、各種遙控器、電視、音響等,這些東西若是受到特定電磁波的影響,就可能會收不到訊號、聽不到音樂、看不到影像,甚至許多電器用品還會如同靈異事件般的自行開啟、關閉等不受控制。在交通安全上,車輛同時也是佈滿電磁波且仰賴電磁波的精密儀器,為了避免這些電磁波互相干擾,Toyota 汽車於 1979 年建立第一座電磁相容測試廠,進行車輛電磁波測試。直至 2009 年 4 月為止,Toyota 於日本已擁有 8 座電磁測試廠。
電磁相容測試主要可分為「Immunity 被動干擾免除」與「Emission 主動干擾免除」兩項目。簡單的說,也就是防止車輛被干擾 (Immunity) 與避免車輛去干擾它者 (Emission) 的被動與主動關係。在「Immunity 被動干擾免除」測試內,主要檢測當車輛在被各種電磁波包圍時,系統作動是否正常;「Emission 主動干擾免除」測試則為了確保車輛所散發出的電磁波不會影響周遭環境。
測試過程乃將車輛停妥於鐵製方形巨大空間內,室內牆面以纖維材質、吸音材質包覆,鐵製牆體則有助於室內電波的反彈,並防止電磁波外洩。Toyota 所擁有的 8 個電磁波測試廠,依頻率差別各自可發出最小 20M 至最大 100GHz 不等的電磁波。車輛在電磁波測試的過程中,所有人員皆須清空於測試廠內,並以遙控方式,控制車內置有的機器人來操控車輛,為車輛進行加速、減速、定速、電子用品使用等測試,以觀察在複雜電波環境下,車輛是否會受到影響,造成任何功能不良。當然不僅是研發車輛的測試,在車輛使用零件上,如整組電氣系統、電氣部件等,在打造的過程中,亦須經過各自的電磁波測試過程與認證,才可使用於 Toyota 車輛上。
經過電磁相容測試的 Toyota 產品,可進一步確保量產車輛,在道路行駛的安全性,並避免受到外界電波干擾與車輛主動發出的電波去干擾週遭環境,目前電磁相容測試已逐漸列入國際車輛檢測標準內,而台灣市場因應法規規定,也將在 2011 年後將實踐「Emission 主動干擾免除」檢測,並於計畫於 2014 年履行「Immunity 被動干擾免除」檢測。
Toyota 之車輛產品銷售於全世界,消費者駕馭著這些車輛或許遨遊於美國中部平坦且寬敞的高速公路上;或許行駛在東歐以石磚拼成的起伏路面,然為了讓全球消費者皆能使用到懸吊品質相同的車輛,Toyota 於日本總公司廠區內建置了 3 套 Road Simulator System 道路模擬試驗機。該項機器利用液壓機構直接連接車輛懸吊結構,並以立體六動向手臂持續操作、擠壓、震動車輛懸吊,來測驗懸吊系統之耐久、極限測試。每輛車在架入道路模擬試驗機後,便會進行持續一週的無間斷測試,利用極度嚴苛的測試過程,來檢視 Toyota 車輛懸吊系統。
然道路模擬試驗機之六動向手臂並非毫無邏輯的持續作動著。其作動內容乃利用六動感知蒐集器,於全球各地道路蒐集路況資訊,建檔進入模擬機系統內。如此一來便可回溯各地路況至極限測試之中。車輛測試過程,會分成荷重測試 (模擬車輛有承載人員與貨物),與無荷重測試,如此一來才可蒐集更為合理的測試後資料。
疲勞耐久測試的優點在於道路模擬試驗機不僅可模擬全球各地路況,並且在風雨無阻的情況下進行長時間測試,不僅節省了許多資源上的耗費,在人力、物力上亦無需千里迢迢的旅赴各地進行測試。並且道路模擬試驗機長達一個禮拜的耐久試驗,亦是人力駕駛難以達成的艱鉅任務。
而在疲勞耐久測試結束後,Toyota 廠內工程師便會開始就車輛上裝載的感應器進行資訊解讀,分析車輛懸吊特性與經過耐久測試後缺失與檢討。本項檢討就不僅僅止於底盤懸吊部分的檢測,而是進行整部車輛的總檢查,以確保經過長時間操練下的產品,是否有能力通過疲勞耐久測試。
實驗室內疲勞耐久測試的實體路駕版-試驗道路耐久測試。當疲勞耐久測試主要用以檢測車輛的底盤懸吊品質、耐用度時,那麼試驗道路耐久測試,更重視的則是了解一部新產品在道路行駛上的整體表現,細節從車輛組裝、NVH 噪聲、振動與懸吊表現。因此 Toyota 利用各種路面型態的打造,建構出各式各樣的坡度路面、礫石路面、磚拼路面、泥濘路面等,經由一次又一次的試駕,來分析車輛性能。
在這個部分就是最直接的人與車輛的互動展現,無須經由任何機械儀器輔助,在 Toyota 廠內試車手親自體驗這輛新產品的能耐。因此經過長時間研發、製作而出的新產品,會在本關卡中接受嚴格挑戰。特別需要重視的焦點在於,車輛懸吊特性、組裝品質與 NVH 表現,在試車手經過專屬流程測試之後,不僅提供意見的回饋,車輛還會經過拆解程序,來檢驗各組件的測試結果。
針對排氣系統的品質檢測項目,Toyota 會於車輛之內架入機器人,進行車輛點火啟動、加速、煞車等動作,在長時間的引擎運作下,檢視車輛排氣系統的品質與功能。目前 Toyota 在全日本共有 64 具排氣分析系統,每日分析車輛里程數總合可超過 1,500 公里,並於一年 365 天當中無停擺的持續測試著。
品質為車輛打造之本,經過 Toyota 所安排的 Quality Insurance System in R&D Process 研發期實踐的車輛保障系統中 7 大測試項目,以完整的流程初步實踐車輛品質之控管。也因此,Toyota 產品銷售至世界各地,亦能擁有同樣的產品水準,在溫差極大的中東沙漠地區,Toyota 的 SUV 產品市佔率近達 4 成,而在嚴寒的冰島地區,Toyota 品牌車輛則有 2 成市佔率。品質雖是一部好車必備的條件,然安全更是不容忽視的標準,在下個章節我們將為您介紹 Toyota 車輛安全打造過程。