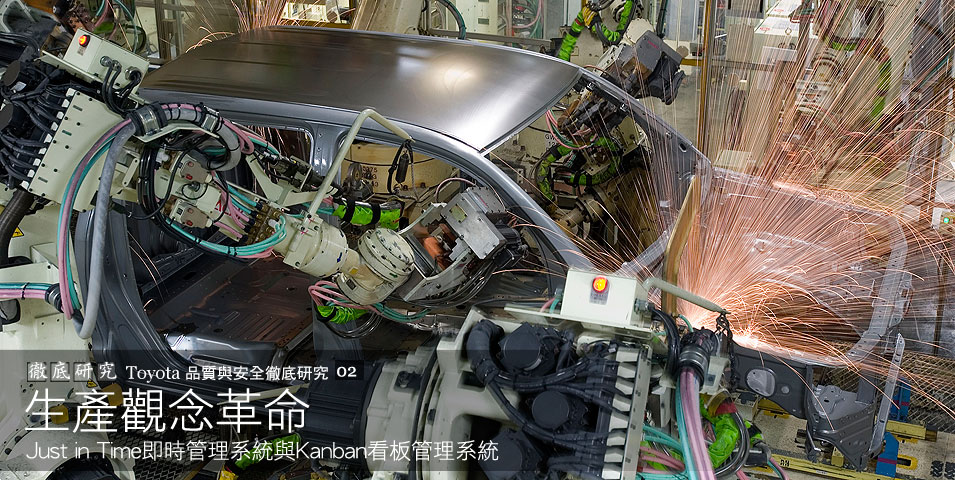
139,178
2010
11月
29
撐起「Toyota Production System,TPS 豐田生產系統」的兩大中心:Just in Time(簡稱 JIT)即時管理系統與 Kanban 看板管理系統,其實都是 Toyota 汽車創辦人 Kiichiro Toyoda 豐田喜一郎早年在父親的豐田自動織機製作所擔任生產部門常務經理時,觀察紡織機工廠作業流程、並交由過去也曾經在豐田自動織機製作所任職的 Toyota 汽車副總裁 Taiichi Ohno 大野耐一實踐在汽車生產線上的生產作業方式。簡單來說,JIT 就是「只在有需要的時候,生產需要數量的產品」,而「看板」則是為了實現 JIT 所誕生的管理與改善工具。
Toyota 自動車工業株式會社於 1937 年 8 月正式由豐田自動織機製作所獨立出來後,由於初期只是一家擁有 300 多名員工的企業,而且跟本沒有實際生產汽車的相關經驗,加上日本當時經濟狀況並不好、日本民眾對汽車的需求量不高,所以 Model AA 剛開始量產時,雖然想仿效美國 Ford 汽車之大批量生產線規劃,但市場需求量跟本不適合採傳統大批量生產設計,且生產效率極低,只有 Ford 生產線的 10 分之 1,所生產的汽車品質亦參差不齊。
於是很快地,當豐田喜一郎在工廠開工的隔年發現了這個狀況後,很快地便看到了生產線上的浪費,於是他便決心想辦法要去縮減生產線上的工作流程,並降低零件、材料輸送過程的時間損耗,以及庫存的閒置,而為了實現這個目標,他第一個想到的,便是當年他在豐田自動織機製作所工作時,紡織工廠內、可以有節省時間與庫存浪費的即時作業流程。
傳統製造業、如美國 Ford 汽車等所採用的大量生產模式,其實就是以加快生產速度、用以大量降低成本,但是若產品發生問題時,卻無法好好解決。甚至為了維持生產線的運作,即使產品需求下滑,仍不得不繼續生產,導致倉庫裡賣不掉的存貨便會越來越多。
而源自豐田自動織機製作所內的這套即時作業流程,是以透過「減少浪費」來替企業「獲取最大利潤」作為經營目標,而所謂的浪費,便是「會使成本增加的生產要素」,也就是所有一切與生產有關、卻不會帶來任何附加價值的過程,包括:紡織原料及布匹成品的庫存、製作過程中所造成的人員或原料搬運動作、生產機器的前置作業準備,以及不良品的產生等等;也因此,「浪費」其實通常都是因為不當的管理所造成,所以要減少浪費,唯有透過生產線上完整且能夠即時反應生產流程的管理系統。
曾在豐田自動織機製作所工作、受這套管理觀念影響很深的豐田喜一郎,當下便決定捨棄最初原想仿效美國 Ford 的大批量化生產流程,並把這套管理系統帶進了起步並不順遂的 Toyota,並在 1953 年時,由副總裁大野耐一提出、解決這套原本並不適合大批量生產方式與即時現場管理的「Just in Time 即時管理系統」。
Just In Time 即時管理系統,簡稱 JIT,是一套能夠有效減少生產成本的管理系統,能夠永遠只保持適當的原料與成品在庫,在恰當的時候生產出恰當數量之成品,比一般傳統單一產品大批量的生產方式,更適合市場規模較小或需求多樣化的市場,也能夠提高產品的競爭力。
JIT 能夠有效節省成本浪費的原理其實很簡單,因為它是以「生產準時」為中心,所以凡是會對生產時間(包括進度超前與落後)造成影響的,都被 JIT 視為可能的浪費,所以在規劃生產線與生產流程時,除了需要精準控制每日產能與需求量外,故障的設備、多餘的人員都得進行淘汰、調整,並採用調整更機動的月計劃與日計劃,儘可能地使半成品在各組裝站停留的時間接近,減少生產線上的閒置時間產生,好讓每一站作業之間的半成品動線可以更順暢、更均衡,而這部分在 JIT 中,被稱為「均衡化」。
值得一提的是,JIT 還有一些非常特別的設計,例如:當市場上的需求增加時,生產線可以很簡單地調整勞動力或設備的運作時間,所以需求增加時,便可靈活地提升產能,而若是需求降低,則可採減班等方式來降低產品產量。此外,JIT 也非常強調「持續改進」,所以就算生產線上一切運作正常,但負責生產管理的工程師與產品設計師仍需不斷精進生產流程與產品,增加可模組化的作業、持續降低浪費、減少工作站與工作站間的閒置時間,並減少準備時間,逐步實現「不良品-零、庫存-零、浪費-零」的目標。
另一個 JIT 與一般生產流程不同的重點,則是它改變了傳統生產過程從原料開始的工序流程,改以根據當天預期所需完成的產品產量而向前規劃工序,可以讓生產單位明確地掌握產量及生產進度,並讓工作站依產品的「看板」來向前個工作站提領原料、生產,但這個「看板」又是甚麼呢?
雖然剛開始時只是工廠生產線上一塊簡單到不行的紙板,記錄著產品的生產型號與規格、生產的流程,以及搬運和運送時的重點,但其實若沒有這塊看起來毫不起眼的 Kanban(看板),恐怕便無法實現豐田喜一郎及大野耐一的 Just in Time 即時管理系統。
由於 JIT 改變了傳統生產過程從原料開始的工序,改以從產品向前規劃的工序,需要從最後一道工序向前推到上一道工序,所以在信息傳遞時,工作站與工作站之間,就需要透過所謂的「看板」來溝通工作內容、產品流向、生產時間、目的地、放置場所、搬運工具等資訊。因此一旦生產計劃確定後,管理負責人就要向各工作站下達生產指令,並在看板上詳細記載產品生產流程與製程,且讓後方的工作站向前方的工作站下達指令,最後才向倉庫與採購單位下達相對應的需求。而且看板必須隨時放在產品旁邊,很清楚地可以讓生產線上的員工知道現在與下一道工序,「沒有看板不能生產,也不能運送」,基本上也就是以看板來決定產量。
至於看板的種類,JIT 系統則是將它分為三大類:生產看板、傳送看板和臨時看板。
![]() |
所謂的「生產看板」,就是一直在產品旁邊的看板,上面會詳細記載這個產品的型號、規格,以及上面該裝有哪些配件,「傳送看板」則是產品在工作站間如何流動的依據,也就是前一個工作站完成產品組裝後,要將產品送往哪個工作站,或產品完成後需送往哪裡的指示,至於所謂的「臨時看板」,顧名思義就是設備要維護、修理,以及生產線突然接獲臨時增產指示時的看板,可用來協助生產線完成非計劃內之產品或設備維修等任務。
事實上,雖然只是一塊小小的板子,但對於 JIT 系統來說,看板絕對具有舉足輕重的關鍵影響力,因為 JIT 是相當獨特的生產管理系統,截然不同於需要透過大批量生產才能減少成本的舊式生產模式,需先規劃出預期產量與工序、流程,才會開始生產,所以才需要「看板」來幫助生產單位精準的掌握生產線進度與設備與員工的效率,兩者相輔相成,也讓 JIT 成了目前最特殊的生產方式,並吸引許多學者開始投入這套系統的研究。最後甚至進化成今天所有管理學院學生的必修科目:「Toyota Production System,TPS 豐田生產系統」,也讓 Toyota 在成立短短 70 幾年後,便成就了豐田佐吉與豐田喜一郎的夢想:由「日本第一」成為「世界第一」。