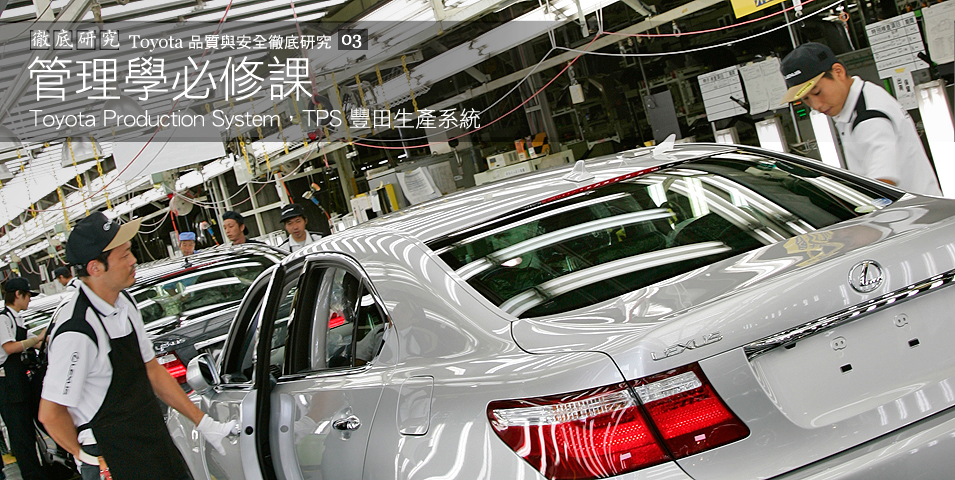
158,628
2010
11月
29
豐田生產系統(Toyota Production System,TPS )又名豐田式生產管理(Toyota Management),是日本 Toyota 汽車副總裁 Taiichi Ohno 大野耐一所建立現代化生產管理模式,不但結合了豐田集團的 Just in Time(簡稱 JIT)即時管理系統與 Kanban 看板管理兩大系統,且加入高度自動化生產與生產制度落實與規劃,並已逐漸發展成一套完整包含企業經營理念、生產單位組織、物流及品質管理、成本控制、程式庫存管理和生產單位管理的作業體系,能夠有效降低企業的生產成本、提高生產效率,且逐步改善產品的生產品質,是目前最受矚目的企業管理理論之一,也是今天所有管理階層及管理學院學生都需要深入了解的必修科目。
![]() |
豐田生產系統的原理與架構,其實說穿了一點也不復雜,就是透過豐田集團著名的 Just in Time(簡稱 JIT)即時管理系統與 Kanban 看板管理兩大系統,並以大量自動化生產模式,降低生產成本、提高效率,並逐步提更產品水準。
如同我們在前一篇文章中所提,Just In Time 即時管理系統,是一套以「生產準時」為最高準則,透過「看板」居中協調,並由產品端向原料端提供需求的生產方式,所以能夠有效減少生產成本的管理系統,可以永遠只保持適當的原料與成品在庫,在恰當的時候生產出數量剛剛好之成品,嚴格控管「浪費」的產生,且比一般傳統單一產品大批量的生產方式,更適合市場規模較小或需求多樣化的市場。
而且除了能夠協助管理階層更輕鬆地掌握成本,由於 JIT 在規劃生產線時,生產線上的員工在控制每日產能與需求時,還被賦予了「自主管理」的任務,所以只要一發現產品品質、數量或機械發生異常問題時,任何人當下都可以立即決定停機、察看,主動排除故障,解決問題,以避免生產線上產生多餘的浪費,並讓工作更有效率。
也由於 Toyota 汽車的豐田生產系統不僅成功地讓它們有效的減少生產成本,且所生產出來之各式產品,在消費者的評價與客戶滿意度調查中,也一直擁有不錯的回應,甚至讓原本僅是「日本第一」的 Toyota,逐步成長成今天的「世界第一」,並吸引國內外各大管理學院紛紛開課研究箇中奧秘,美國知名工業工程管理學教授 Jeffrey Liker 還將其生產線的管理理念,重點式的歸納成 14 項原則。
豐田生產系統 14原則 |
|
原則 1: 企業經營與生產線需設立長遠目標 |
|
原則 2: 採用「向前的生產流程」 |
|
原則 3: 建立流暢的作業流程 |
|
原則 4: 工作均衡化 |
|
原則 5: 發現問題,即時暫停 |
|
原則 6: 工作標準化 |
|
原則 7: 借重「看板」 |
|
原則 8: 採用最適當的生產技術 |
|
原則 9: 培養真正了解企業文化的員工 |
|
原則 10: 強調團隊合作 |
|
原則 11: 重視合作夥伴 |
|
原則 12: 親臨現場了解情況 |
|
原則 13: 提出並解決 5 個 W |
|
原則 14: 不斷檢討,持續改善 |
|
拜貫徹豐田生產系統所賜,今天的 Toyota 汽車,不但已是全球最知名、生產量最大的汽車品牌之一,採納這套生產管理模式的德國 Porsche、國內生產 Giant 自行車的全球自行車龍頭產業「巨大」,也都有效地較過去降低了生產成本,並獲得了極大的成功。也難怪豐田的這套生產系統會成為當前最受矚目的企業管理理論之一,並成為各大企業體管理階層與各管理學院學生都必需花時間了解的必修科目。